California’s regulator for workplace safety is set to approve new protections for preventing heat illness at indoor facilities. But the cost to cool down processing facilities—which only operate for about two months of the year—would reach as high as to $9 million, according to an industry estimate.
“It's extremely expensive,” said Roger Isom, president and CEO of both the California Cotton Ginners and Growers Association and the Western Agricultural Processors Association (WAPA), during a recent presentation to the standards board governing the Division of Occupational Safety and Health, or Cal/OSHA. “It comes down to one word: feasible.”
Isom explained the organization’s proactive efforts to address worker safety, which often extend beyond the state’s existing regulatory requirements. In partnership with other agriculture associations, WAPA and Cotton Ginners train workers “up and down” the Central Valley on preventing and treating heat illness. Every member company has an action plan to prepare for any emergencies. Once a year, Isom and his team survey the members on injuries, running through a list of about 30 questions that tease out details like the time of the shift, who was assigned where, years of experience, and so on, analyzing every accident that was reported.
Board member Laura Stock, a UC Berkeley public health researcher, worried that some of those workers may have been too fearful of retaliation to report indoor heat illness symptoms. Isom responded that the workers have reported outdoor heat issues and even minor problems like spider bites, but never complained of indoor heat since the organizations began the surveys in 1994.
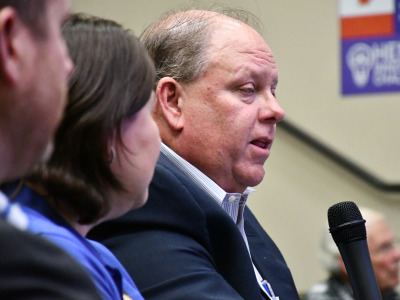
But Isom did worry about maintaining the same level of safety while incorporating the new requirement to cool buildings down to 87 degrees.
“When you add up all the things we're doing now—between nighttime lighting requirements and all the other trainings—it's taking our eye off the ball on where we really need to emphasize our safety efforts,” he said.
The injuries tend to involve failing to follow lockout procedures for machinery, not incorporating fall protections or avoiding safety protocols for aerial lift equipment.
But his greatest issue with the proposed regulation remained its feasibility. To cool one cotton gin facility, the cost of installing a massive air conditioning unit and sealing up the building would start at $1 million and run up to $1.5 million. The steep energy costs for running the unit would add further ongoing expenses. For companies to install units in multiple facilities, such as for a large walnut processor in the Sacramento Valley with 10 buildings, it would add up to $3.5 million to $9 million.
In the case of cotton ginners, the cost would mainly cover protections for just two or three workers. The gins operate in the cooler months of late fall and early winter. During the hot summer months, typically just a couple workers perform repairs, starting their day as early as 5 a.m. at the upper reaches of the building and working their way eventually down to the cooler pits and basements by the time the afternoon heat arrives, according to Isom. Fans, portable coolers and five-gallon water jugs follow along. Similar to a proposed requirement in the draft regulation, the facilities offer air-conditioned break rooms to cool down.
When ginning, the wide warehouse doors remain open. Closing them to turn on air conditioning units would suck in the walls of the 36,000 square-foot buildings. Cotton gins use compressed air to power the pneumatic system, propelling the lint and seed through the processing. Fans up to 12 feet in diameter move large volumes of air at up to 300,000 cubic feet-per-minute, explained Isom. The whirling breeze allows outside workers to come inside and avoid the hot sun, while enabling the companies to comply with Cal/OSHA’s longstanding outdoor heat illness prevention standard.
It’s easy to sign up for a FREE month of Agri-Pulse news! For the latest on what’s happening in Washington, D.C. and around the country in agriculture, just click here.
“We don't see a tremendous amount of benefit in terms of worker safety in our operations,” said Isom of the proposed indoor standard. “This isn't a very enclosed warehouse or an enclosed container.”
Walnut hullers, meanwhile, rely on dehydrators that heat the nuts to about 100 degrees following the initial wet stage of processing. An employee opens and closes the vents and gates to draw in the next walnuts while dropping the processed ones down to a conveyor belt. Setting the temperature to 87 degrees for that worker would not sufficiently dry the walnuts.
At the hearing, Steve Johnson, who directs safety for Associated Roofing Contractors, noted that adding so many air conditioning units to cool a building would create other unintended consequences. Such facilities are often noisy, and the units would add much more to the cacophony.
“I've been around them before when we tried to cool warehouses down. You can't have a conversation in front of it,” said Johnson. “When you try to solve one problem, sometimes you bring in another problem.”
For more news, go to Agri-Pulse.com.